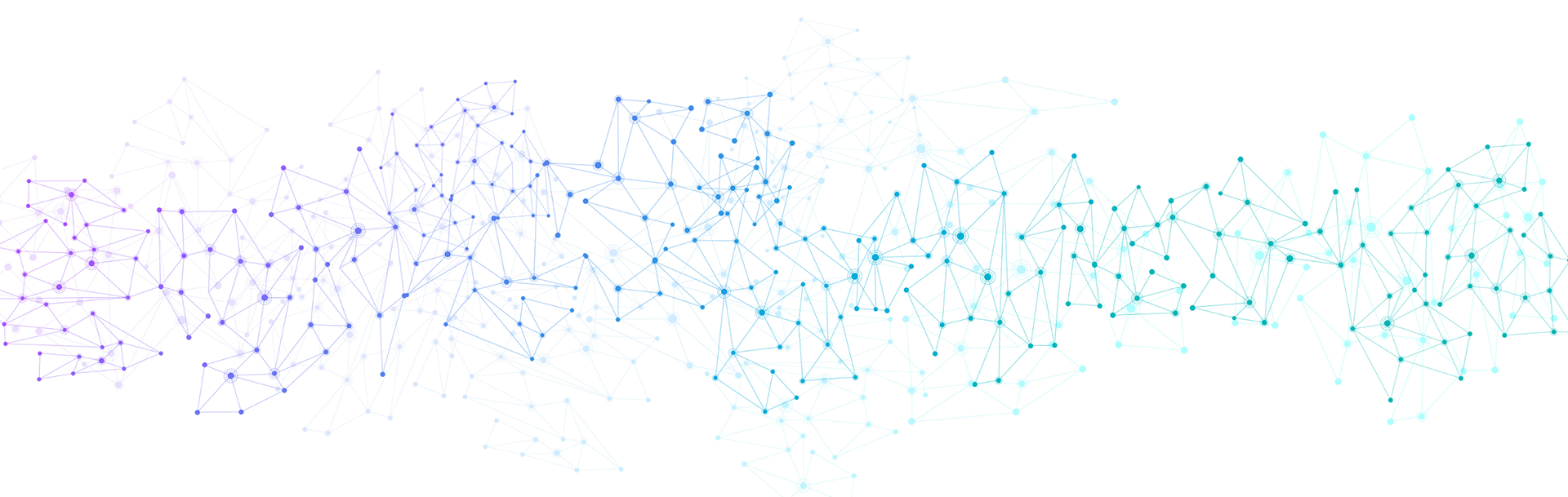
FA
(Factory Automation)
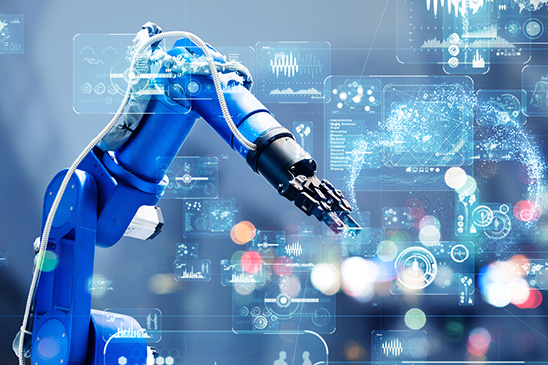
Co-creating the new factory for the IoE (Internet of Everything) society with customers
"Maintenance-free" Manufacturing Lines through WPT
In manufacturing industry, where customers seek for FA (factory automation), stoppage of production line due to frequent disconnection of wires of sensors placed around moving parts causes a large amount of opportunity loss.
For example, an automotive production line can generate economic value worth about 3 million yen (30 thousand dollars) per minute, but when the production line halt caused by broken sensors occurs, its opportunity losses can lead to several hundred million yen (million dollars).
Moreover, sensors on manufacturing equipment are so dependent on wiring that it's difficult to install sensors in hard-to-wire locations and that it inhibits flexible changes in sensor layout.
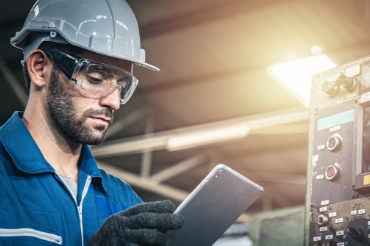
Features of Aeterlink's Technology (AirPlug™︎)
Aeterlink's WPT (wireless power transfer) system "AirPlug™︎" enables maintenance-free installation of sensors in locations where there are frequent wire disconnections around moving parts or wiring is difficult, and real-time acquisition of information through high-speed data communication.
We would like to work with you to create a new sensor network that transcends physical limitations.
Long-distance Power Supply with High Eenergy Efficiency
Our WPT technology has made it possible to supply several mW of power to a distance of more than 10 meters, while the limit of transmission distance of traditional WPT technology was just 50 centimeters. We are the first in the world to provide long-distance power supply technology on a practical level.
No Angle Dependence
The omni-directional antenna enables power feeding to "moving objects" that are moving or rotating.
It can also supply power to sensors equipped with "moving parts."
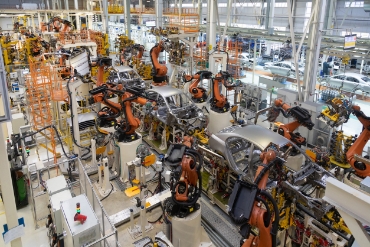
Environmentally Adaptive Antenna
We provide smaller products based on our expertise in WPT technology for medical devices such as pacemakers that are implanted in the human body.
We have several product lineups of multiple antenna shapes to meet requirements that differ depending on product.
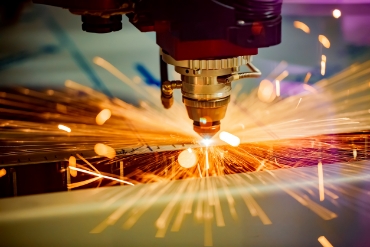
High-speed Data Communication
Our technology has enabled frequent data communication in every 5 millisecond with low power consumption, with real-time information acquisition.
In addition, we have also developed edicated IC chips for power receivers so that they can be applied to a wide range of products.
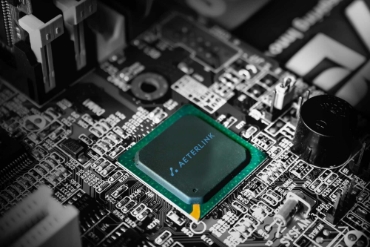
Why Aeterlink?
Why is the WPT technology essential for FA?
Increasing number of sensors = Increasing number of power supply objects
In addition, manufacturing industry is more advanced in implementation of "Digital Twin" using sensors than other industries. In addition, manufacturing industry is more advanced in implementation of "Digital Twin" using sensors than other industries.
In order to improve the quality of production and increase the flexibility of manufacturing processes, the amount of sensing objects and data is expected to increase exponentially in the future.
"IoE (Internet of Everything) society" will be the keyword for the next era. The 6G standard, scheduled to be launched in 2029, is based on the premise of the IoE society, and its standardization has already been started in each country. In the IoE society, everything will be connected to the internet. For example, sensors will be attached not only to moving parts but also to everything, including finished products and work-in-progress. The collected data will be analyzed by AI to visualize and optimize the production process.
"Power supply" is the biggest bottleneck in FA
There are three phases to build FA systems as follows:
- Data collection
- Data visualization/prediction
- Mutual control by information processing system
- Data collection
"Power supply" is bottleneck - Data visualization/prediction
- Mutual control by information processing system
In the first phase, "1. Data collection," sensing and data transmission to the network is required, meaning some form of "power supply" is necessary.
We see one of the major obstacles in this "Data collection" phase is "power supply."
Traditionally, in the field of FA, most of power supply for production equipment has relied on wiring. As a matter of fact, however, it imposes a heavy burden on manufacturing site such as stoppage of production lines and maintenance management caused by broken wires. Furthermore, technologies such as energy harvest using sunlight cannot provide power supply enough to cover all production lines due to small amount and instability of their power generation.
These approaches of power supply, in a sense, are the result of "forcible" realization of sensor implementation. Furthermore, as mentioned above, the number of sensing objects will increase exponentially in the future. It is virtually impossible to implement them using conventional power supply methods, and there is no doubt that "power supply" will become even more apparent as a bottleneck in FA.
Case Studies
NEDO
We developed a mid-long range WPT and data transmission technology for FA robot sensors, which was selected for the NEP (NEDO Entrepreneurs Program) in 2020 and the STS (Seed-stage Technology-based Startups) in 2021.
Voice of Customer: Major Sensor Manufacturer A
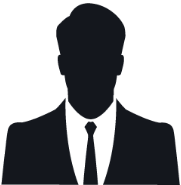
Person in charge of Technology Development